Апстракт:Аутор анализира производњу и потрошњу игличастог кокса у нашој земљи, перспективе његове примене у индустрији графитних електрода и материјала за негативне електроде, како би проучио изазове развоја производње игличастог кокса из нафте, укључујући недостатак сировина, невисоки квалитет, дуг циклус производње и прекомерну процену примене, повећање истраживања сегментације производа, примене, мера учинка, као што су студије асоцијације за развој тржишта високог квалитета.
Према различитим изворима сировина, игличасти кокс се може поделити на нафтни игличасти кокс и игличасти кокс од угља. Нафтни игличасти кокс се углавном производи од FCC суспензије путем рафинирања, хидродесулфуризације, одложеног коксовања и калцинације. Процес је релативно сложен и има висок технички садржај. Игличасти кокс има карактеристике високог садржаја угљеника, ниског садржаја сумпора, ниског садржаја азота, ниског садржаја пепела итд., и има изванредна електрохемијска и механичка својства након графитизације. То је врста анизотропног висококвалитетног угљеничног материјала са лаком графитизацијом.
Игличасти кокс се углавном користи за графитне електроде ултра велике снаге и катодне материјале за литијум-јонске батерије. Као стратешки циљеви „угљеничног врха“ и „угљенично неутралности“, земље настављају да промовишу трансформацију и модернизацију индустрије гвожђа и челика и аутомобилске индустрије, прилагођавање индустријске структуре и промовишу примену енергетски штедљиве нискоугљеничне и зелене технологије заштите животне средине, како би се промовисала производња челика у електролучним пећима и брзи развој возила на нову енергију. Потражња за сировим игличастим коксом такође брзо расте. У будућности, низводна индустрија игличастог кокса ће и даље бити веома просперитетна. Ова тема анализира стање и перспективе примене игличастог кокса у графитним електродама и анодним материјалима и износи изазове и контрамере за здрав развој индустрије игличастог кокса.
1. Анализа производње и правца тока игличастог кокса
1.1 Производња игличастог кокса
Производња игличастог кокса је углавном концентрисана у неколико земаља као што су Кина, Сједињене Америчке Државе, Уједињено Краљевство, Јужна Кореја и Јапан. У 2011. години, глобални производни капацитет игличастог кокса био је око 1200 кт/год, од чега је производни капацитет Кине био 250 кт/год, а постојала су само четири кинеска произвођача игличастог кокса. До 2021. године, према статистици Синферн Информатион, глобални производни капацитет игличастог кокса ће се повећати на око 3250 кт/год, а производни капацитет игличастог кокса у Кини ће се повећати на око 2240 кт/год, што ће чинaти 68,9% глобалног производног капацитета, а број кинеских произвођача игличастог кокса ће се повећати на 21.
Табела 1 приказује производни капацитет 10 највећих произвођача игличастог кокса у свету, са укупним производним капацитетом од 2130 кт/год, што чини 65,5% глобалног производног капацитета. Са становишта глобалног производног капацитета предузећа за производњу игличастог кокса, произвођачи игличастог кокса из нафтне серије генерално имају релативно велике размере, просечан производни капацитет једног постројења је 100 ~ 200 кт/год, док је производни капацитет игличастог кокса из угља само око 50 кт/год.
У наредних неколико година, глобални капацитет производње игличастог кокса ће наставити да расте, али углавном из Кине. Планирани и у изградњи у Кини капацитет производње игличастог кокса је око 430 хиљада тона годишње, а ситуација са прекомерним капацитетом је додатно погоршана. Ван Кине, капацитет игличастог кокса је углавном стабилан, а руска рафинерија ОМСК планира да изгради постројење за игличасти кокс капацитета 38 хиљада тона годишње у 2021. години.
Слика 1 приказује производњу игличастог кокса у Кини у последњих 5 година. Као што се може видети на слици 1, производња игличастог кокса у Кини је достигла експлозиван раст, са сложеном годишњом стопом раста од 45% за 5 година. У 2020. години, укупна производња игличастог кокса у Кини достигла је 517 хиљада тона, укључујући 176 хиљада тона угља и 341 хиљада тона нафте.
1.2 Увоз игличастог кокса
Слика 2 приказује ситуацију увоза игличастог кокса у Кини у последњих 5 година. Као што се може видети на слици 2, пре избијања COVID-19, обим увоза игличастог кокса у Кини значајно се повећао, достигавши 270 хиљада тона у 2019. години, што је рекордно висок ниво. У 2020. години, због високе цене увезеног игличастог кокса, смањене конкурентности, великих залиха у лукама, а уз то и континуираног појављања епидемија у Европи и Сједињеним Државама, обим увоза игличастог кокса у Кину у 2020. години износио је само 132 хиљада тона, што је пад од 51% у односу на претходну годину. Према статистици, од увоза игличастог кокса у 2020. години, увоз нафтног игличастог кокса износио је 27,5 хиљада тона, што је пад од 82,93% у односу на претходну годину; Угаљ мери игласти кокс 104,1 кт, 18,26% више него прошле године, главни разлог је тај што је поморски транспорт Јапана и Јужне Кореје мање погођен епидемијом, друго, цена неких производа из Јапана и Јужне Кореје је нижа од цене сличних производа у Кини, а обим поруџбина низводно је велики.
1.3 Упутство за примену игличастог кокса
Игличасти кокс је врста висококвалитетног угљеничног материјала, који се углавном користи као сировина за производњу графитних електрода ултра високе снаге и вештачких графитних анода. Најважнија поља терминалне примене су производња челика у електролучним пећима и батерије за возила са новом енергијом.
Слика 3 приказује тренд примене игличастог кокса у Кини у последњих 5 година. Графитне електроде су највеће поље примене, а стопа раста потражње улази у релативно равну фазу, док материјали за негативне електроде настављају брзо да расту. У 2020. години, укупна потрошња игличастог кокса у Кини (укључујући потрошњу залиха) износила је 740kT, од чега је потрошено 340kT негативног материјала и 400kt графитних електрода, што чини 45% потрошње негативног материјала.
2.1 Развој производње челика електронском AF методом
Индустрија гвожђа и челика је главни произвођач емисије угљеника у Кини. Постоје две главне методе производње гвожђа и челика: висока пећ и електролучна пећ. Међу њима, производња челика у електролучној пећи може смањити емисију угљеника за 60%, и може остварити рециклажу отпадног челика и смањити зависност од увоза гвоздене руде. Индустрија гвожђа и челика предложила је да преузме водећу улогу у постизању циља „угљеничног врха“ и „угљеничне неутралности“ до 2025. године. Према смерницама националне политике индустрије гвожђа и челика, постојаће велики број челичана који ће заменити конверторски и високопећни челик електролучним пећима.
У 2020. години, производња сировог челика у Кини је износила 1054,4 милиона тона, од чега је производња електролучног челика око 96 милиона тона, што чини само 9,1% укупног сировог челика, у поређењу са 18% светског просека, 67% просека у Сједињеним Државама, 39% у Европској унији и 22% производње електролучног челика у Јапану, постоји велики простор за напредак. Према нацрту „Смерница за промоцију висококвалитетног развоја индустрије гвожђа и челика“ који је издало Министарство индустрије и информационих технологија 31. децембра 2020. године, удео производње електролучног челика у укупној производњи сировог челика требало би да се повећа на 15% ~ 20% до 2025. године. Повећање производње електролучног челика значајно ће повећати потражњу за графитним електродама ултра велике снаге. Тренд развоја домаћих електролучних пећи је висок клас и великих размера, што доводи до веће потражње за графитним електродама великих спецификација и ултра велике снаге.
2.2 Статус производње графитне електроде
Графитне електроде су неопходан потрошни материјал за производњу челика електродизајнираног поклопца (eAF). Слика 4 приказује производни капацитет и излаз графитних електрода у Кини у последњих 5 година. Производни капацитет графитних електрода повећан је са 1050kT/год у 2016. години на 2200kt/год у 2020. години, са просечном годишњом стопом раста од 15,94%. Ових пет година је период брзог раста производних капацитета графитних електрода, а такође и текући циклус брзог развоја индустрије графитних електрода. Пре 2017. године, индустрија графитних електрода као традиционална производна индустрија са високом потрошњом енергије и високим загађењем, велика домаћа предузећа за графитне електроде смањују производњу, мала и средња предузећа за графитне електроде суочавају се са затварањем, а чак су и међународни гиганти у производњи електрода морали да зауставе производњу, препродају и изађу. 2017. године, под утицајем и вођењем националне административне политике обавезног укидања „челика за подне шипке“, цена графитних електрода у Кини је нагло порасла. Подстакнуто вишком профита, тржиште графитних електрода је увело талас обнављања и ширења капацитета.
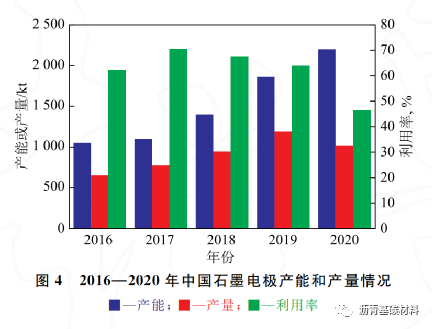
У 2019. години, производња графитних електрода у Кини достигла је нови максимум у последњих неколико година, достигавши 1189kT. У 2020. години, производња графитних електрода смањена је на 1020kT због ослабљене потражње изазване епидемијом. Али у целини, кинеска индустрија графитних електрода има озбиљан вишак капацитета, а стопа искоришћења је смањена са 70% у 2017. на 46% у 2020. години, што је нова ниска стопа искоришћења капацитета.
2.3 Анализа потражње за игластим коксом у индустрији графитних електрода
Развој електродизајничког челика (eAF) ће подстаћи потражњу за графитним електродама ултра високе снаге. Процењује се да ће потражња за графитним електродама бити око 1300 кт у 2025. години, а потражња за сировим игластим коксом око 450 кт. Пошто је у производњи графитних електрода и спојева великих димензија и ултра високе снаге, игласти кокс на бази нафте бољи од игластог кокса на бази угља, удео потражње за графитним електродама за игластим коксом на бази нафте ће се додатно повећати, заузимајући тржишни простор игластог кокса на бази угља.
Време објаве: 23. март 2022.